Nick Hutchinson, CEO of Glider Technology, discusses the hidden costs of poor handover information in construction and the pressing need for a digital-first approach to meet evolving regulatory and sustainability requirements
Having spent many years working on the commissioning and handover of large, complex buildings around the world, I know that accurate information sits at the heart of a successful project.
As the construction industry tightens its margins and faces increasing regulatory scrutiny and sustainability demands, the disconnect in how data transitions from construction into operation is an increasing concern.
The time has come to embrace a digital-first approach to handover information management that meets both current and future requirements.
Growing regulatory and sustainability pressures
Recent years have seen significant changes in building regulations and a stronger focus on sustainability. Safety requirements, stricter health and safety guidelines and the growing need for compliance with environmental standards place a greater emphasis on data transparency and asset information. Therefore, the need for accurate, reliable and easily accessible building information is more critical than ever.
Contractors and asset owners not only need to ensure they meet compliance requirements but also must demonstrate that the building is safe, efficient and environmentally responsible.
This requires comprehensive information management, where every detail, from O&M manuals to health and safety files and Regulation 38 documentation, is captured and maintained in a way that facilitates smooth operations and sustainability efforts.
Paying multiple times for the same data
The data collected during the construction phase is meant to provide the foundation for a building’s safe and sustainable operation. However, poor handover information management at this stage often leads to financial implications and inefficiencies.
Contractors frequently pay for the same documentation twice when information initially created during planning, design and construction is collated by third-party O&M production companies during the handover stage. This adds substantial and unnecessary costs. During the building’s operational phase, FM teams may need to resurvey the property to collect asset data required for compliance and planned preventative maintenance (PPM).
The causes of cost duplication
This issue is the result of outdated practices, fragmented systems and a lack of standardisation in managing information during design, construction and handover.
Although we’ve moved into the digital age, many traditional processes have not fully adapted and could be simplified with more-streamlined digital workflows.
During design and construction, data gets passed between multiple systems, using a variety of formats, creating a fragmented information environment.
Even when Common Data Environments (CDEs) are used, they sometimes remain disconnected from the handover process, requiring the data to be recollected and verified. This lack of integration not only inflates costs but also delays project timelines and compliance with evolving regulations.
The industry also suffers from inconsistent standards for gathering and formatting information, making the production of O&M manuals more time-consuming and costly than it needs to be.
This leads to data that is difficult to work with during and after handover, hindering the ability of FM teams to efficiently mobilise their teams and manage building safety and sustainability measures.
When there is a disconnect between construction and FM teams, information does not transition seamlessly. FM teams expend additional effort to compile and verify data post-handover, leading to delays in meeting safety and sustainability compliance.
While the Soft Landings framework, developed by BSRIA, aimed to bridge this gap, its limited application in practice has left a void between construction completion and operational use.
While Building Information Modeling (BIM) has made significant strides in addressing these inefficiencies, there still needs to be a more integrated approach that directly ties BIM and information management into the digital handover process, in line with evolving regulatory and sustainability requirements.
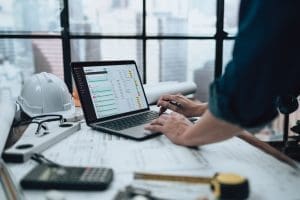
A digital-first approach
The solution lies in a digital-first approach that integrates handover information into the design and construction process from the outset.
By capturing, validating and structuring data digitally, contractors can ensure the information is ready for seamless handover and use by FM and operational teams, eliminating the need for re-collection and re-verification.
This approach reduces the risk of defect claims by providing a clear, accurate record of as-built data. When contractors can demonstrate what was delivered, they are better positioned to defend against potential defect claims, thereby protecting their slim profit margins.
For asset owners, this comprehensive, structured data is invaluable for operating the building safely and efficiently. Detailed handover information allows owners to verify the quality and condition of assets. This contributes to the building’s long-term value and helps meet regulatory and sustainability goals.
The role of integrated platforms
Addressing these inefficiencies requires not just a change in mindset but also the right tools.
Selecting a digital platform that supports the entire lifecycle of an asset can make the difference between a tick-box exercise and creating a reliable data source that adds value throughout the building’s lifecycle. This value extends from design and construction to operation and eventual decommissioning, ensuring compliance with both current and future regulations.
When properly configured, digital platforms can align seamlessly with digital workflows, formatting and integrating data collected during design and construction for direct use by FM and operational teams.
This integration ensures that information remains accessible and useful, not just during handover but throughout the building’s operational life. Furthermore, this digital approach makes it easier to adapt to changing regulatory landscapes and sustainability benchmarks.
A futureproof approach for a changing industry
As project margins continue to tighten and regulatory demands increase, contractors can no longer afford to overlook the hidden costs of poor handover information.
By adopting a digital-first approach, handover data is more accurate, complete and valuable for the building’s entire lifecycle. This not only reduces costs but also enhances building safety, environmental performance and long-term value – benefitting both contractors and asset owners.
This collaborative approach gives contractors a competitive edge, allowing them to exceed client expectations, streamline compliance and win more work in the future.
Now is the time to move away from outdated practices, effectively integrate digital technologies and standardise our processes to meet evolving industry demands. In doing so, we can transform handover from a costly burden into a value-adding component of every construction project, one that is fully aligned with today’s regulatory and sustainability requirements.